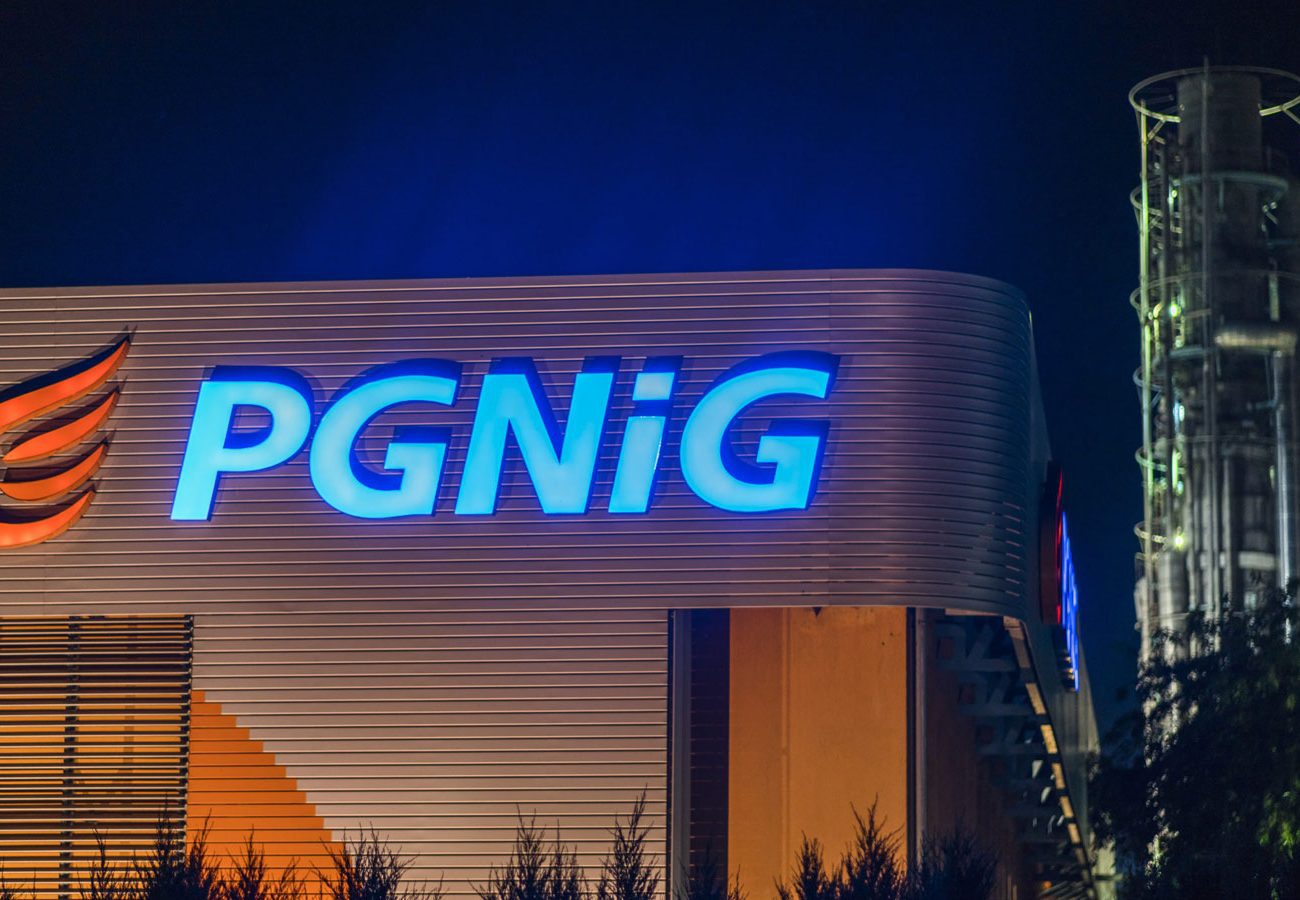
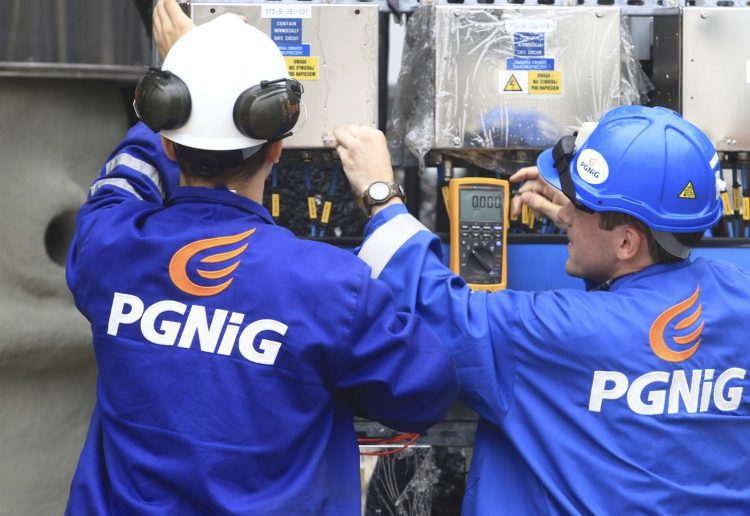
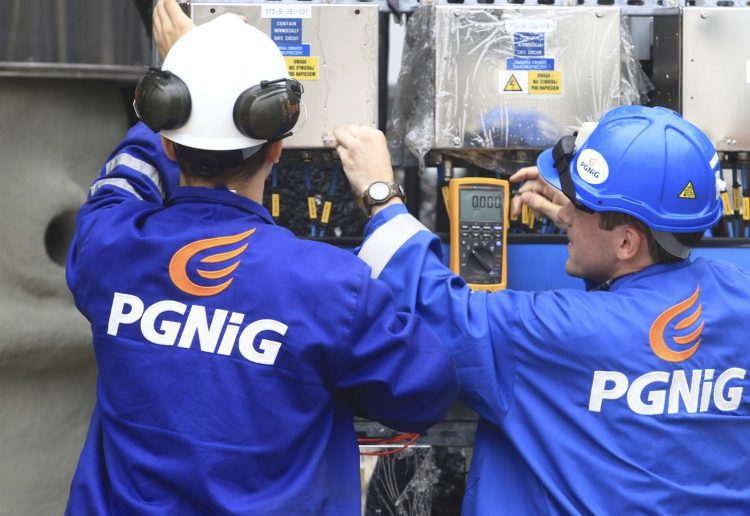
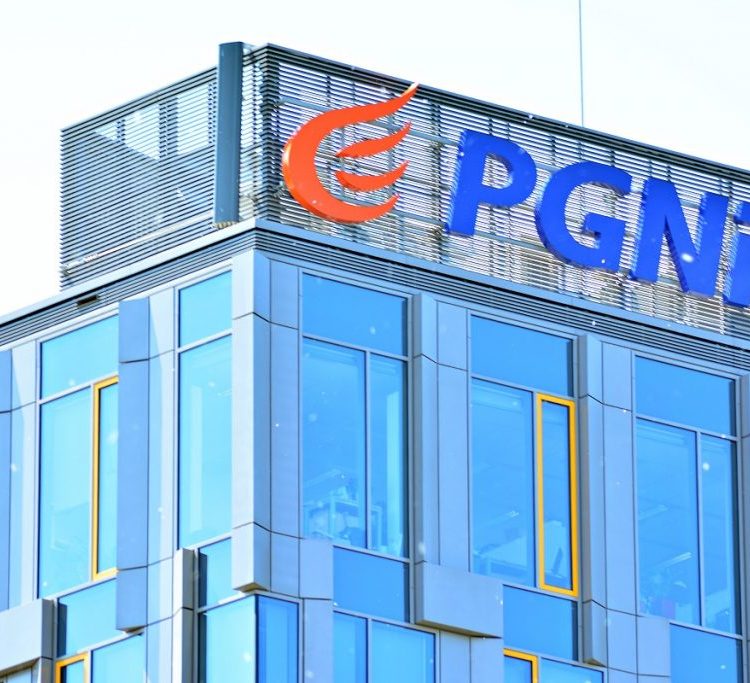
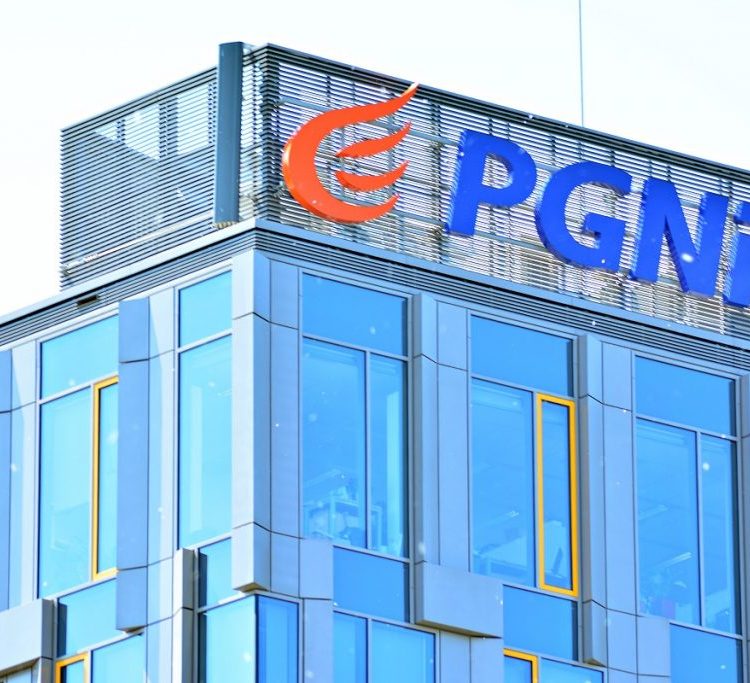
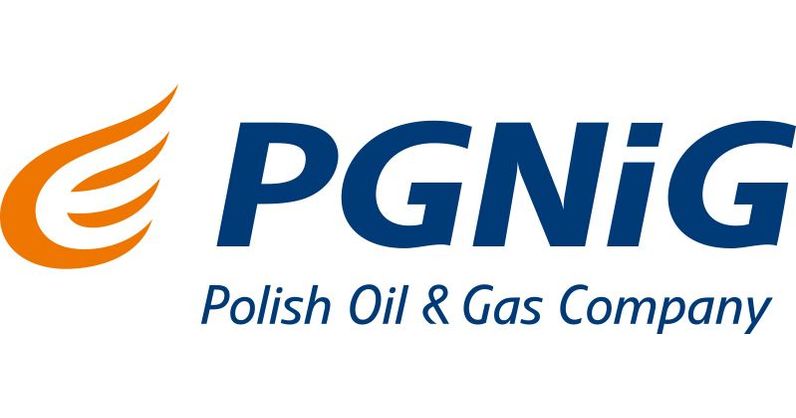
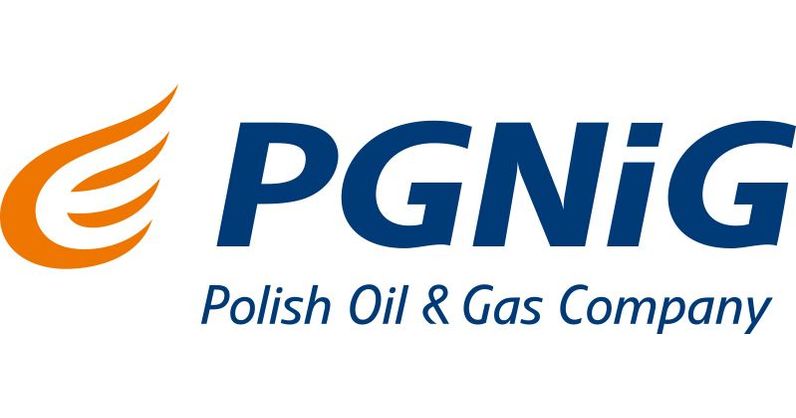
PGNiG
Overview
In 2024, PGNIG, a leading operator in the energy and heating services sector, implemented a modern platform designed to streamline the execution of contracts and enhance cooperation with raw material suppliers. Integrated with in-house solutions since 2015, the platform enabled logistics, purchasing, and planning teams to manage contracts efficiently, while optimising delivery schedules and supplier interactions.
Objectives
The main objectives of this project were:
-
Develop a platform that integrates seamlessly with PGNIG’s in-house systems, facilitating contract execution and supplier collaboration.
-
Improve operational planning for cooperation with raw material suppliers, considering both long- and short-term contracts.
-
Optimise delivery schedules, facilitate traffic planning, and manage plant demand with the help of a dynamic stocking policy.
The Challenge
PGNIG faced several key challenges in managing its supply chain and supplier relations:
-
The need for a dynamic operational plan that could handle the complexities of cooperating with multiple raw material suppliers.
-
Managing a robust stocking policy that needed to balance the fulfilment of long- and short-term contracts with supply chain restrictions and plant demand.
-
The challenge of optimising delivery planning and traffic to ensure seamless supply while avoiding delays or inefficiencies.
-
Efficient record-keeping and synchronisation with existing ERP systems to ensure that all operational data was accurately captured and utilised.
The Solution
To address these challenges, a comprehensive supply management platform was developed, integrating key operational processes. The solution focused on:
-
Supply Management System:
The platform was designed to manage the supply of raw materials efficiently, allowing for better coordination between PGNIG and its suppliers. It supported the execution of contracts in both long and short terms, ensuring stock availability met the operational requirements. -
Delivery Planning and Traffic Optimisation:
The system facilitated optimised delivery planning, ensuring the smooth flow of materials while minimising traffic congestion and logistical inefficiencies. This allowed PGNIG to meet plant demand effectively, without unnecessary delays. -
Efficient Recording and Synchronisation:
The platform featured robust record-keeping capabilities, ensuring that all data related to contract execution, deliveries, and supplier collaboration was accurately tracked. This information was synchronised with PGNIG’s existing ERP systems, providing a unified view of operations.
Results and Benefits
The implementation of the modern platform delivered several critical benefits to PGNIG:
-
The creation of an integrated platform that streamlined collaboration between logistics, purchasing, and planning teams, allowing them to execute contracts seamlessly.
-
Improved operational planning, enabling PGNIG to manage raw material supplies effectively, balancing long-term and short-term contracts with plant demand and logistical constraints.
-
Optimised delivery schedules and traffic planning, leading to more efficient supply chain management and reduced operational bottlenecks.
-
Accurate and efficient record-keeping, with synchronisation to ERP systems, ensuring that all aspects of contract execution and supplier cooperation were monitored and managed effectively.
By implementing this modern platform, PGNIG was able to enhance its supply chain operations, improve supplier relations, and achieve greater efficiency in contract execution, contributing to its continued leadership in the energy and heating services sector.